BY LOGAN WEBB
When designing a parking structure, the first decision that needs to be made is what structural material will be selected. Structural material on most parking garages will represent 50% of your total budget. There are three primary options to consider: Cast-in-place (CIP) concrete, steel framed, and precast concrete. Each one of these building materials has its own advantages and disadvantages.
The first material you can consider is precast concrete. Almost all garages that can be constructed using precast concrete are currently precast because of its architectural versatility, reduced construction time, and managing risk on job sites.
Because precast concrete is produced off-site in controlled conditions and cast face down to the form, which allows for high architectural capabilities. This allows precast concrete garages to match the surrounding architecture in an area more easily than with cast-in-place or steel. In addition, since these pieces are produced off-site, this allows for shorter on-site construction schedules. Precast allows job sequences that historically have needed to be done sequentially to now happen in parallel with one another. This is because precast concrete facilities are manufacturing the structure while items such as foundations are being completed on the job site. Once the job site is ready for installation, pieces can be shipped out and construction can start immediately.
Now having said this pre-cast concrete also has its disadvantages. Some of the most noticeable disadvantages would be reduced interior spaces, and some potential for higher maintenance costs. Pre-cast pieces usually have to follow a pre-engineered standard and because of this many times you will have less flexibility in making the interior of your garage have an open floor plan. Often times you will see pre-cast parking garage have associated cast-in-place elements such as curbs, and foundations. Because these elements can typically not be achieved with pre-cast elements.
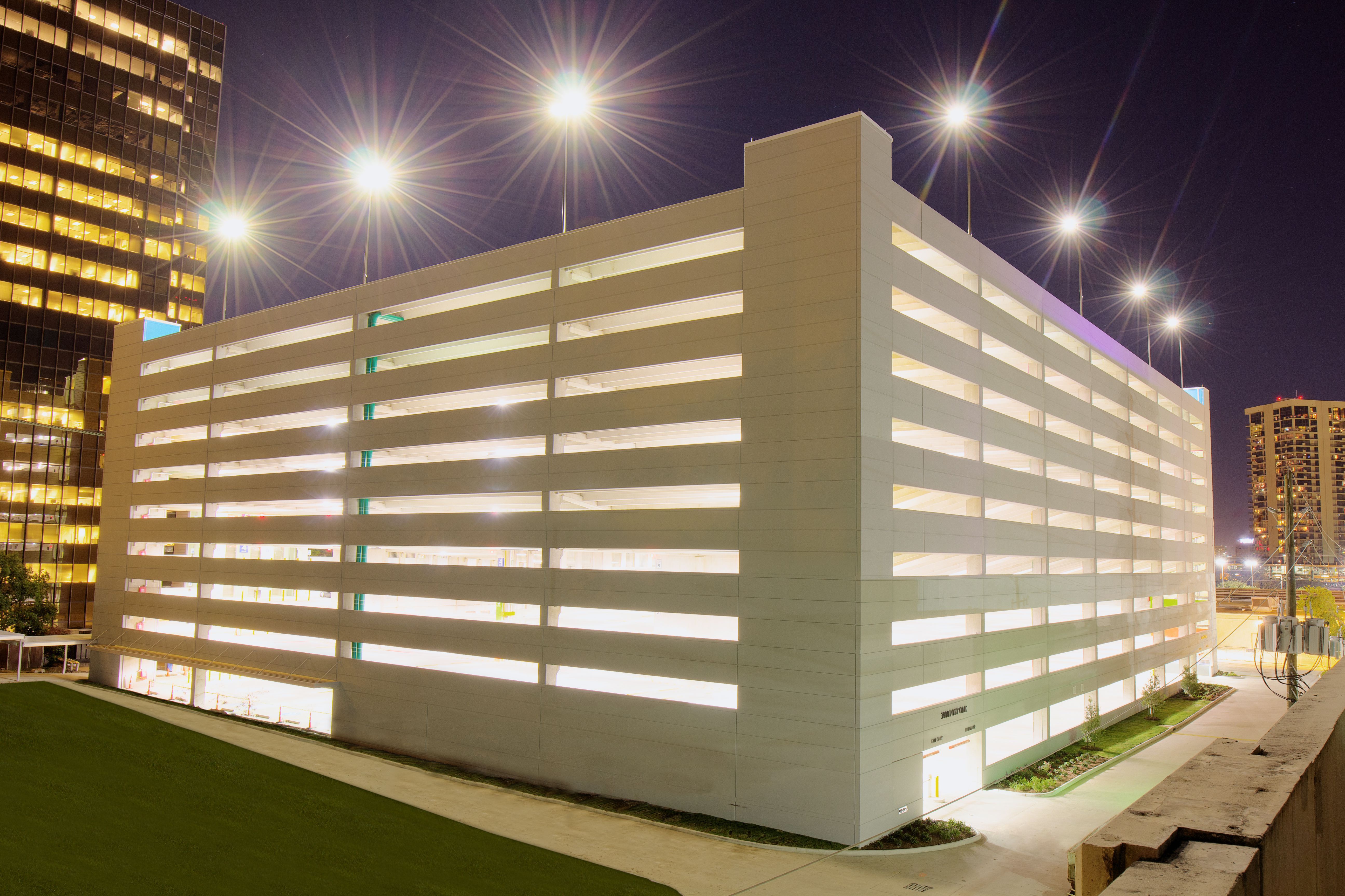
The next material designers typically consider is a cast-in-place systems one of the main advantages of a cast-in-place system would be the open floor plan. Because a cast-in-place system uses much larger construction areas with fewer breaks and joints it allows for many more and larger open spaces in your parking structure. This open area often allows for better lighting, and an overall larger feeling to the interior of the garage. This is a direct advantage to precast as precast struggles to maintain open spaces over large distances.
Now one of the most notable downsides to a cast-in-place system would be the higher construction costs, and longer construction times. The primary reason for these downsides is because most if not all the fabrication when erecting a cast-in-place garage has to be done on site. This is because you only have so long before concrete sets up and hardens. This limits options because you will have to ship concrete from some what near by locations for use on your job site. In addition to this you have to spend time waiting for the lower levels of concrete to set before you can start casting on top of it. For these two simple reasons you are looking at drastically increased construction times, and have limited options in pricing due to location restraints.
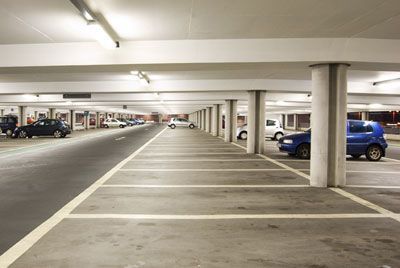
Finally, you could consider a steel framed system, which rely primarily on steel to steel connections. If you wanted to expand your garage you simply can just add on more levels vertically to your garage through steel to steel connections. Along with this advantage like a cast-in-place system you can have very large open spaces in a steel frame garage.
Now one of the disadvantages of a steel framed system comes from using steel itself. Because many times a steel framed parking structure will be exposed to outside elements its has the potential to corrode and rust over time. To prevent this from happening continual maintenance, such as painting and coating all exposed steel beams, will have to be done to ensure the structural integrity of the parking structure remains.
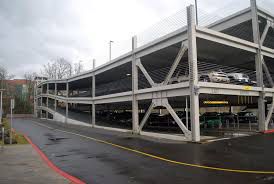